Traction Inverter for (H)EV
Gain up to +20% energy with ACS
Tackling key challenges of e-motors
OEMs are striving to increase the efficiency of the e-motor/inverter by tackling many challenges:
- Deliver a high-efficiency all across the eMotor torque/speed operating range
- Deliver a wider operating range with higher torque and speed range
- Deliver more power with less rare earth material and with less costs
- Reduce the transmission / speed reducer needs and costs
- Rapid fault detection and response time assuring highest levels of safety for the consumer
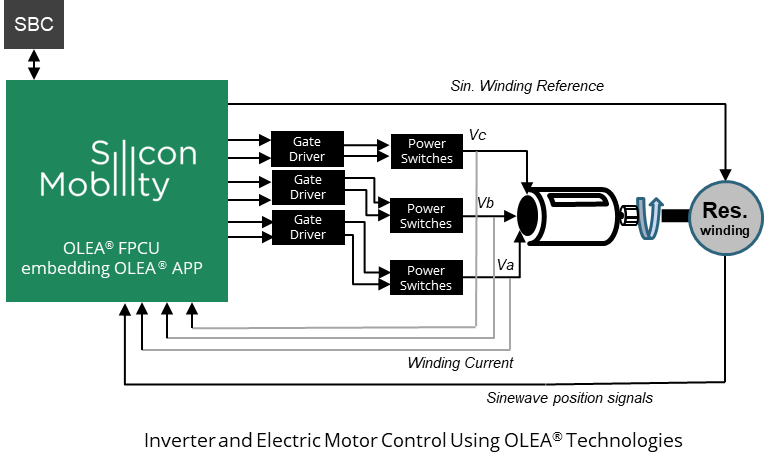
Our Solution for Inverter
We offer a full stack solution to address the e-motor/inverter control application with a powerful system-on-chip and application:
- ACU U310 – A single chip solution for integrated powertrain domain control and energy management
- ACU T222 – Safe, real-time and automotive qualified system-on-chip solution which enables advanced control algorithms
- AC Composer – Model-based application development and calibration framework for ACU
- AC Lib – Rich collection of advanced software and control algorithms optimized for the ACU
- AC App inverter – Scalable software platform for automotive inverter and e-motor control application optimized for the ACU FPC
Key Benefits
- Software flexibility and modularity enabling development of inverter/e-motor control platform
- Support 48V to +800V for HEV and EV
- Support any MOSFET, IGBT, SiC or GaN based inverters
- 100% Model based design accessible as source code
- High efficiency and performance with AC App Inverter
- Up to 20% of energy gain with reduction of switching losses in inverter and reduction of iron losses and coper losses in e-motor
- Up to 30% of e-motor torque/speed range increase
- Up to 50% BoM reduction compare to performance equivalent solutions
Grab your Starter Kit, now.
We offer customer Starter Kits for immediate hands-on experience with our solution. It allows testing and evaluation while enabling fast prototyping and development.
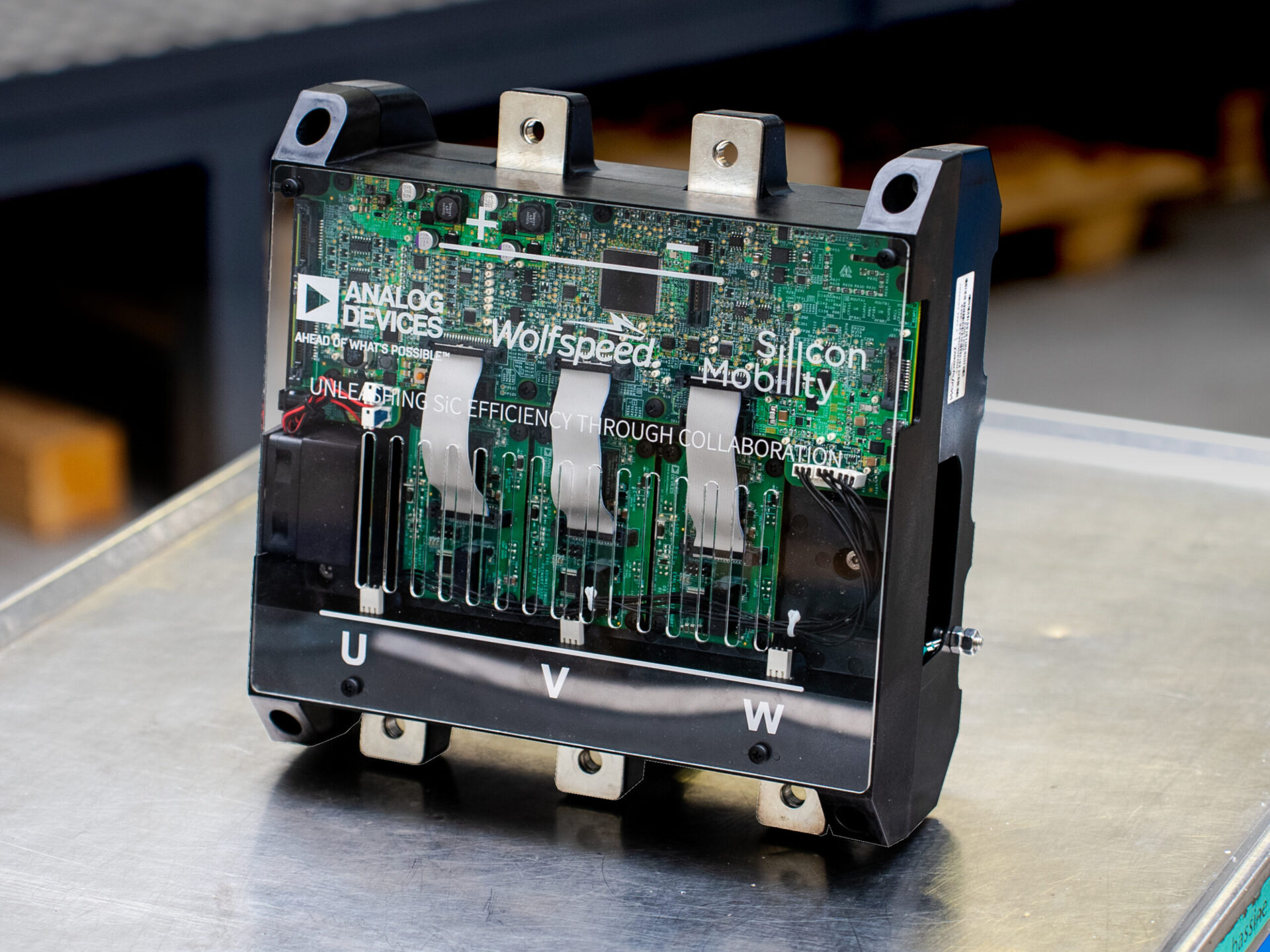
300 kW SiC Inverter Platform
SIC INVERTER Platform with Analog Devices and Wolfspeed
Our best-in-class system-level power density and efficiency obtained by combining ADI’s gate drivers, power, isolation, and signal chain solutions with Wolfspeed’s efficient SiC MOSFET technology and controlling it all with Silicon Mobility’s advanced controller chip and application software.
Features
- CAB450M12XM3 Power modules
- ADuM4177 Gate drivers
- Controller board with
– ACU controller chip
– AC App Inverter configurable e-motor/inverter control application software
– E-motor interface (Tº and position sensors) - Vehicle interface (CAN / USB / UARS / GPIOs)
- DC-LINK Capacitance
Generic T222 Starter Kit
T222 HVIC Starter Kit:
A complete package that includes ACU T222 based development boards and an in-house built AC App Inverter software. It additionally includes documentation for quick application design.
The kit is suitable for HV inverter and e-motor control applications and can be delivered with AC App Inverter for evaluation.
Available with the 176 pins or 100 pins packages versions of ACU T222.
Contact us for more information
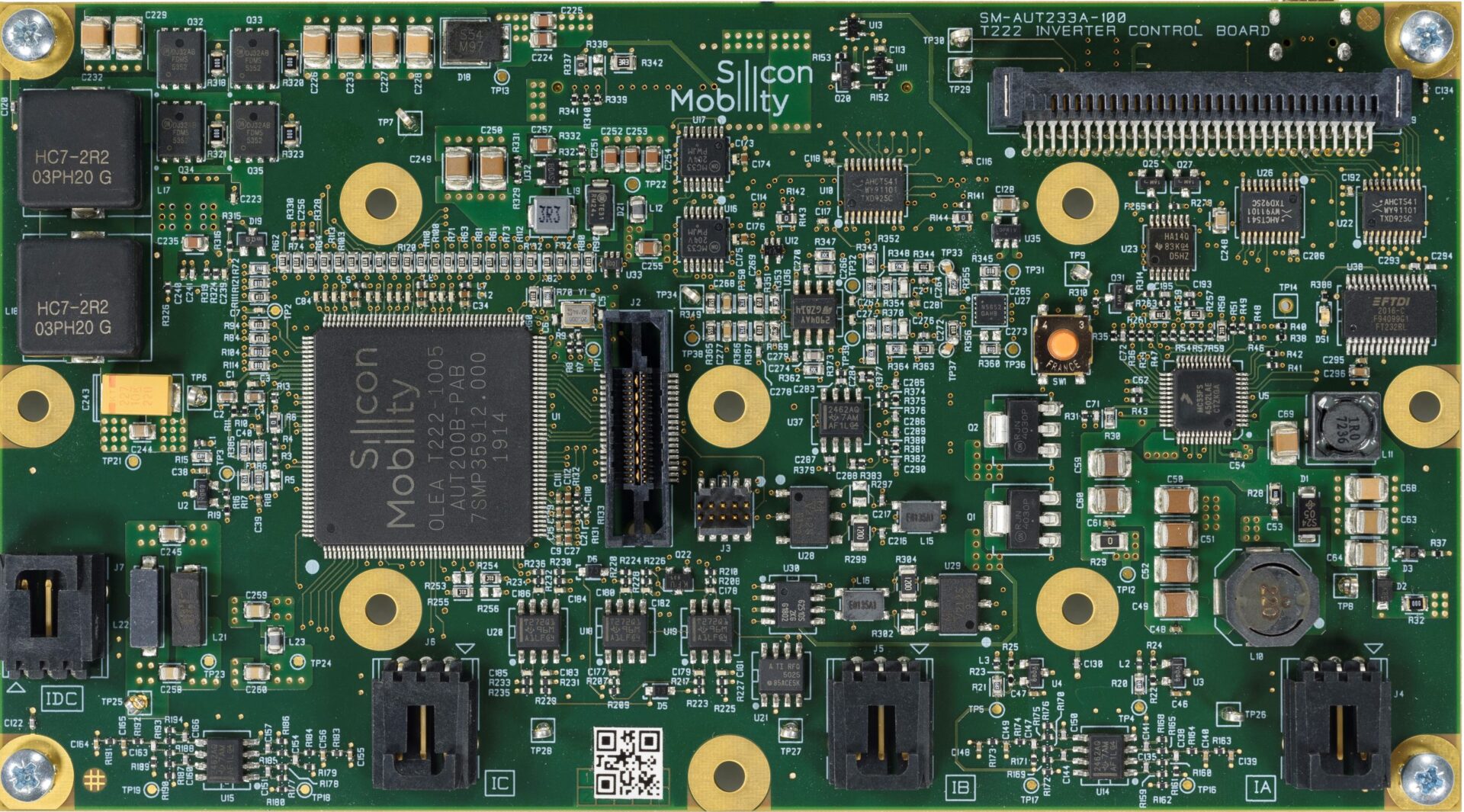
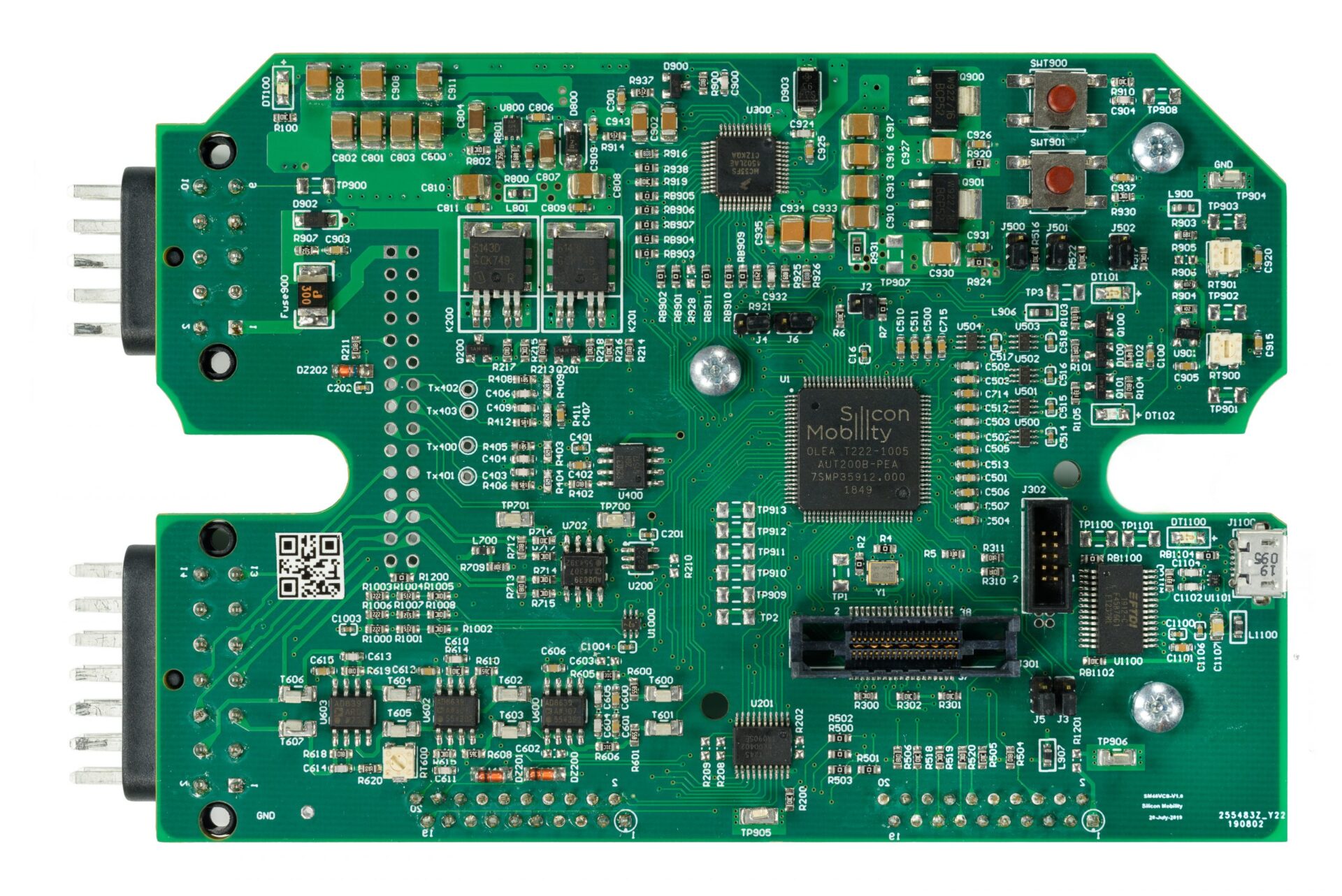
Semikron SKAI3 Inverter module
T222 SKAI3 Starter Kit with SEMIKRON
A complete package which includes ACU T222 Inverter board for Semikron SKAI3 module + AC App Inverter for inverter application development + GUI calibration tool + documentation.
SiC INVERTER
SIC INVERTER Reference Design with CISSOID
Up until now, customers only really had 2 options. The first was to develop all the hardware, then integrate with third party software into their design environment. This was extremely time consuming and required in depth knowledge of SiC-based power system design. The second option was to buy an off-the-shelf inverter that, however, does not offer the ability to fully customise for the application requirements. Now this reference design offers the best of both worlds: fast prototyping and adaptable to the application requirements.
- 1200V SiC-based power module
- Up to 350kW/850V operation
- Integrated Gate Driver board
- Control board with ultra-fast ACU T222
- Supports both SVPWM and DPWM
- ISO26262 ASIL Level D ready
- DC and phase current sensors
- DC link capacitor & EMI filter
- Liquid cooling
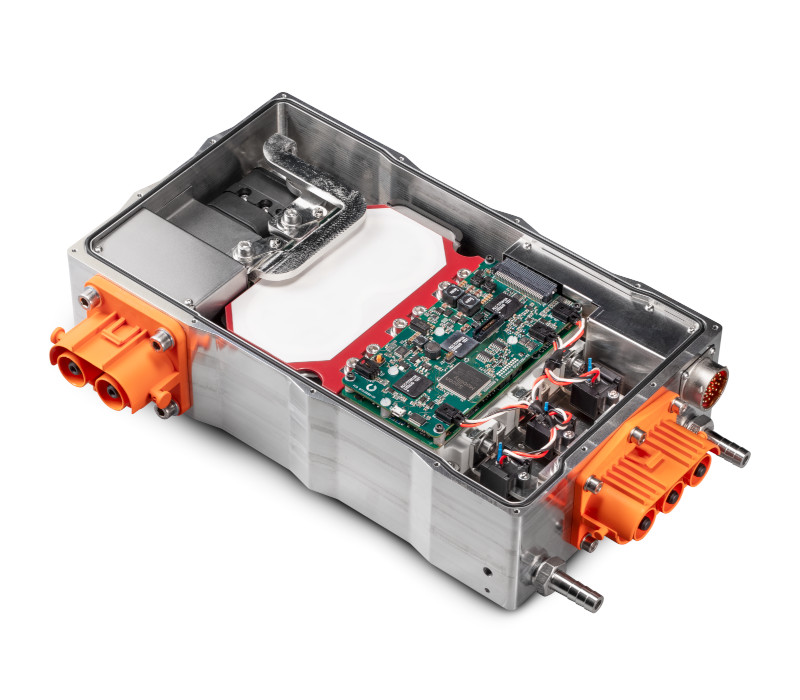