为OLEA® FPCU优化的基于算法的软件
OLEA®LIB被封装成互补的构件,根据客户和应用的需要,提供多个层级的特性和内容。该库内容将作为MATLAB和Simulink的参考和目标模型。OLEA®LIB中的模型可直接用于OLEA®COMPOSER中的MiL仿真和自动代码生成。
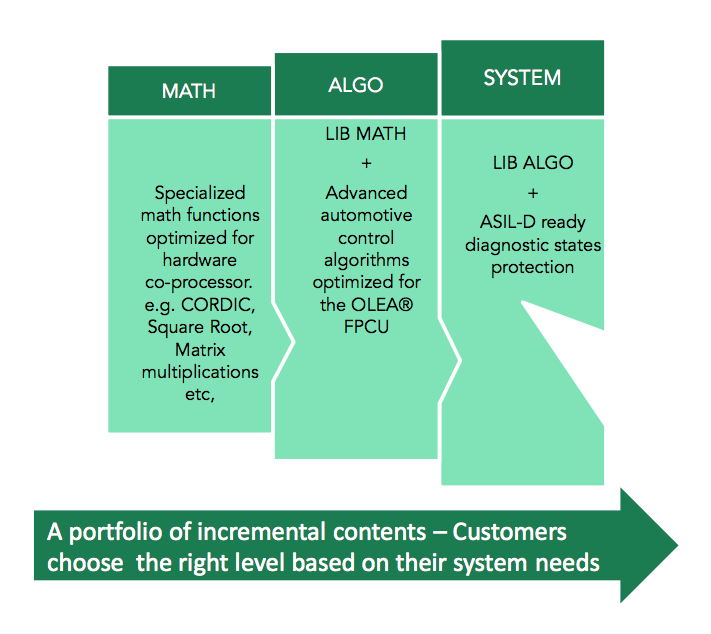
核心优势
更高的性能: OLEA®LIB软件和算法已针对OLEA<sup>®</sup>FPCU进行了优化,并利用现有硬件资源和加速器(数学单元、DSP功能和标准外设)的所有优势,提供可实现的更高性能和集成度。
更短的开发时间:通过使用OLEA<sup>®</sup>LIB,开发人员大大减少了在OLEA® FPCU上开发、优化、测试和标定其算法所需的时间。该数据库中的每个功能都可根据多个参数进行配置,并完全集成到 OLEA®COMPOSER Target Framework。
数据库内容
OLEA® LIB Math | OLEA® LIB Algo | OLEA® LIB System |
---|---|---|
* 坐标旋转数字计算引擎
- 除法运算器 - 平方根运算 - 矩阵乘法器 - PID算法 | - Clarke 电流变换,Park 电流变换
- 去耦和弱磁 - 逆向Park / Clarke 电压变换 - 空间矢量脉宽调制 Id/Iq 控制 - 电机速度调节 - 追踪环路位置估计器(磁阻、旋转变压器等...) - 无传感器位置估计(启动/低速/高速) - 降压-升压DC/DC调节 | 逆变器控制系统功能n
- 基于现场的PMSM或WRSM电机的变频器控制 - 磁场定向控制和空间矢量调制算法。 DC-DC转换器控制系统功能 - Buck-Boost峰值流控制功能 - 支持多达6个并联的DC/DC转换器 |