OLEA® T222 FPCU
1st generation of Field Programmable Control Unit
Key Applications
Optimize a large number of critical, safe, and real-time in-car functions including:
- Electric motor / Inverter control
- High Frequency DC-DC converter control
- On Board Charger (OBC) control
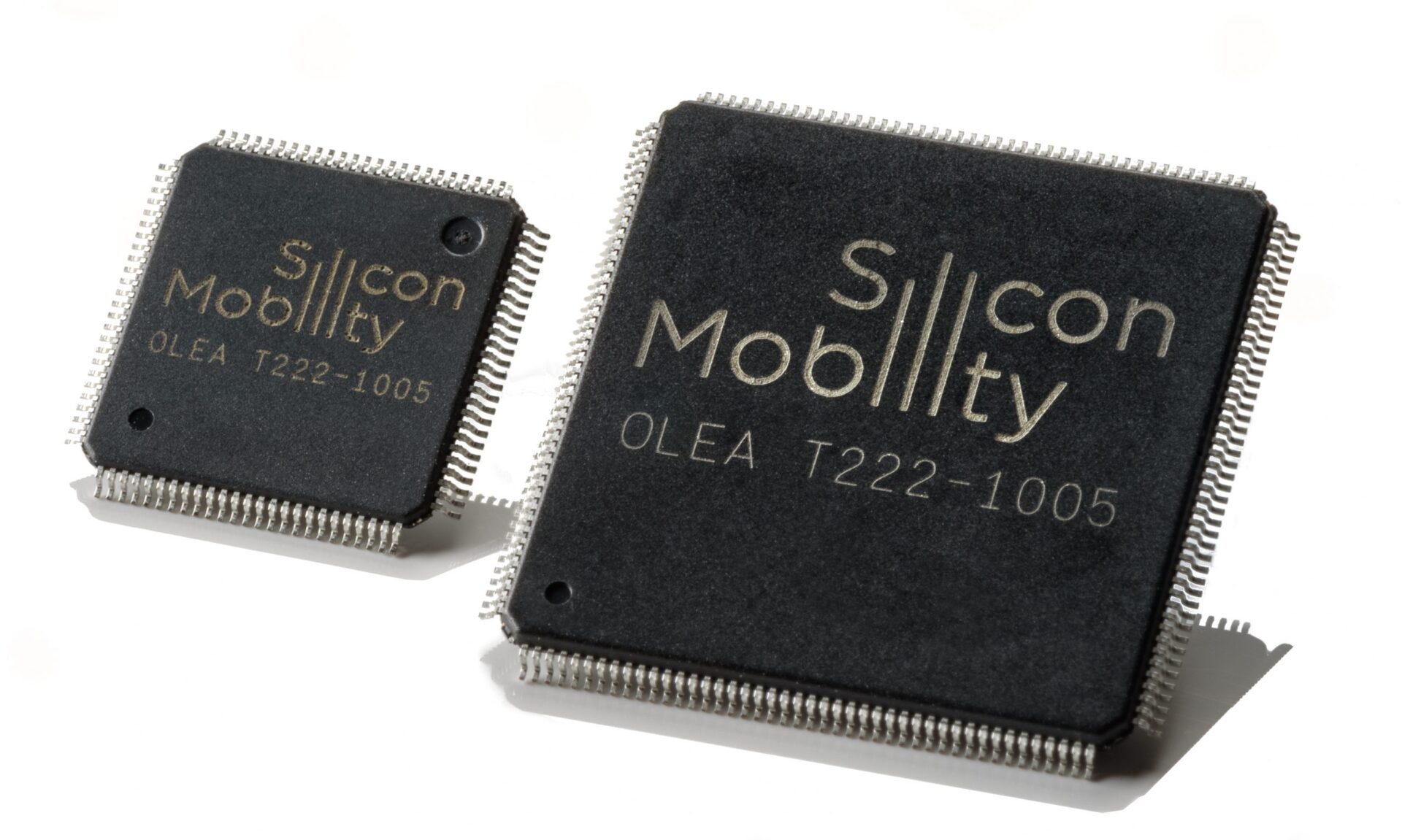
Key Benefits
Flexibility: Programable hardware and software to remove processing bottleneck issues and to enable customization
Real-Time: Timing predictable by design
Safe: Complying with industry safety standards, ensuring both chip level and system level functional safety. Rapid fault detection and corrective/containment actions enables faster turnaround and reaction times for the automotive sub-systems.
Open: Open architecture providing a hardware platform without any software dependency
Reduced BoM and Total Cost of Ownership: Without a need for additional DSP or other FPGA, OLEA®️ T222 FPCU reduces the total Bill of Material, offering direct cost savings for the customers
One of a kind
OLEA®️ T222 FPCU is a member of the OLEA family of automotive control solutions. The OLEA®️ T222 FPCU is the industry’s first Field Programmable Control Unit (FPCU), a new semiconductor architecture combining the hardware flexibility of the AMEC®️ real-time control unit with the software flexibility of a standard processor into a single chip.
AMEC®️ integrates parallel data paths between the acquisition and actuation peripherals and the Flexible Logic Unit (FLU). The FLU is an automotive specific, robust embedded programmable logic with multiple DSP resources. OLEA®️ T222 FPCU also features SILant®️, an ASIL-D functional safety integrated architecture. SILant®️ provides reliable countermeasures against various faults and increases fault coverage all the way upto the application level, without compromising the chip performance.
Unlike multi-core MCU which rapidly experience software bottlenecks, FPCU provides combination of hardware and software processing capability for high frequency, precise and complex control algorithm, while limiting heat dissipation. Using Silicon Mobility’s FPCU, the user’s control command can be programmed in hardware into FLU and delivers the unprecedented performances:
- 40x faster processing compared to legacy solutions
- 1000x faster fault detection compared to legacy solutions
- 125x device heat reduction improving system integration
Unique Technologies
- AMEC®️ FLU: Real-time actuators/sensors control and processing based on programmable logic
- SILant®️: ISO 26262 ASIL-D functional safety solution
Open Architecture
- ARM®️ Cortex-R5F in lockstep
- Embedded Flash
- CAN & LIN Communication ports
Standards Compliancy
- ISO 26262 ASIL-D
- AUTOSAR 4.3
- AEC-Q100 Automotive Qualified
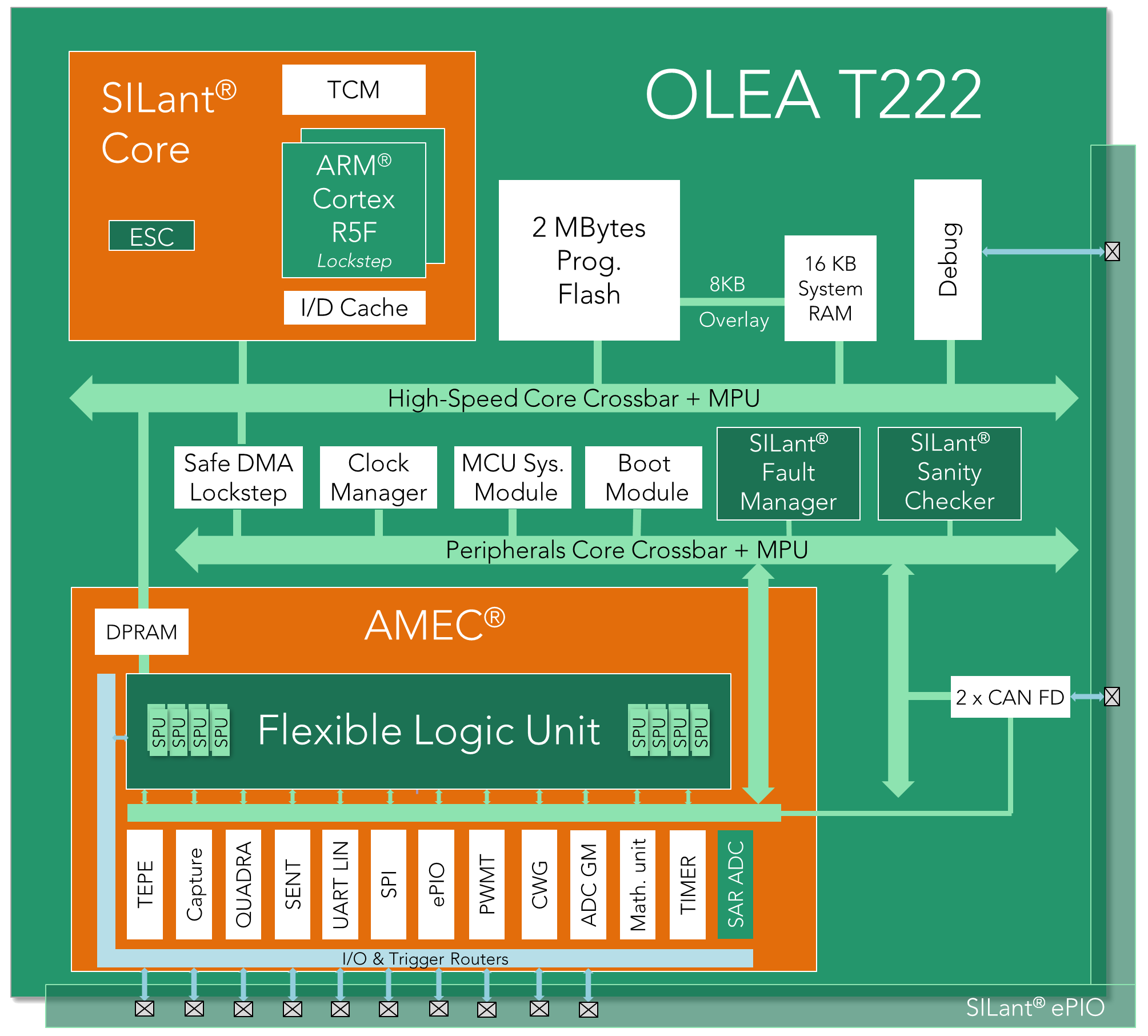
Key Features
Function | Key Features | Benefits |
---|---|---|
Processing | 32-bit ARM®️ Cortex-R5F in lockstep
- 200 MHz operating frequency - 16 KB / 8 KB instruction and data cache L1 with ECC - 64 KB Tightly Coupled - Memory with ECC - Floating point unit - Thumb2 high code density® | High performance CPU for compute intensive automotive applications
Open ARMÆ CPU leveraging a well supported tool chain and 3rd party ecosystem Lock-step mechanism provides highest level of fault detection and correction for safety-critical automotive applications |
Motor Control & Processing | Advanced Motor Event Control - AMECÆ
- Flexible Logic Unit - 4560 Programmable Logic Elements - 20 x 24-bit Signal Processing Units - 200 MHz clock input - 8 KB DPRAM - Parallel access for acquisition & control - Clock Waveform Generator (CWG) with 4 channels - 5 x Pulse Width Modulator (PWM) with 4 channels | A patented and embedded flexible hardware technology
Fast and highly efficient data-processing of real-time critical functions.
Parallel and local processing eliminates the software bottlenecks present in traditional control systems Reduced BOM Cost with integration of DSP units, eliminating the need for additional components |
Safety | Safety Integrated Level Agent - SILantÆ
- ASIL-D architecture and infrastructure - Detecting latent faults - System Events Sequences Controlling (ESC) - End to end ECC transfer - Safe DMA transfers with CRC checks - Protections for , I/O, clock, resets, chip supply - Sanity Checker providing BIST for latent faults in logic/memory - ADC Self-test | Rapid detection and corrective action for faults.
Dazzling fast system level fault detection, correction and containment in tens of nanoseconds. Enables Safe execution of safety critical applications in real-time. |
Actuators and Sensors
& Communication ports | 6 channels Capture
Quad-Encoder Thermal Estimator Position Engine 3 x SENT 2 x SPI with PSI5-S support 3 x UART with PSI5-S support 2 x ADC Group Manager Trigger Router 118-ch Multiplexed General Purpose I/O 33 Programmable Input filters 16-priorities Advanced Generic Interrupt Controller (AGIC) 2 x CAN-FD complying ISO 11898-1:2015 3 x UART-LIN complying LIN 1.3; 2.0 and 2.1 8 x 4 channels 12-bit ADC SAR @ 2MS/s MAX 8 x Analog comparators 2 x Temperature Sensors | High level of flexibility with multiple sensor inputs and I/O options. |
System | 2 MB eFlash with EEPROM Emulation support 24 KB of System SRAM with ECC DMA Controller with CRC providing 16 channels in lockstep mode and 32 channels in DMA split-mode 8 x System Timers Watchdog complying with AUTOSAR 4.2 Fault Manager Unit Interconnect with end to end ECC and Multilayer MPU 50 MHz Internal Ring Oscillator Crystal oscillator input 1-50 MHz Voltage Regulator (3.3V to 1.2V) with bypass Power on Reset with LVD/HVD | High level of reliability with end to end error detection and correction. |
Debug | JTAG and SWD debug ports
Trace Port interface Unit and Embedded Trace Buffer 16 KB Overlay RAM | Improve the debuggability of the automotive subsytem. |
Power supply and Packages | QFP100 and 176
3.3 or 1.2 V for Core supply 3.3 V for I/O supply 3.3 V for ADC supply | Multiple package options provide flexibility for the customers to choose based on the system form-factor requirements. |
Power Consumption & Temp. range | <200 mW
Ambient Temperature Range -40°C to +125°C (AEC-Q100 Grade 1) | Ultra low power consumption ensures that the system operates with minimal power. |